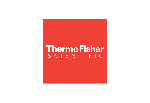
PPI Business System Specialist III
Work Schedule
Standard (Mon-Fri)
Environmental Conditions
Office
Job Description
General Summary
Thermo Fisher Scientific Inc. is seeking a highly motivated individual to join our team as a Process and Automation Specialist. In this role, you will have the opportunity to contribute to distribution and logistics process optimization primarily in our European Distribution Center in Bleiswijk NL with potential to support other regions, to make a significant impact. By applying your understanding of lean principles and automation, you will be instrumental in improving operational efficiency, reducing costs, and improving productivity in our sophisticated and regulated distribution network.
Process Analysis and Optimization
- Conduct detailed analysis of existing processes to identify bottlenecks and propose improvements that will improve efficiency.
- Apply industrial engineering techniques, including time and motion studies, process mapping, and data analysis, to identify areas for optimization.
- Able to gain process optimization through layout and flow change within our distribution centers
- Collaborate closely with various teams to successfully implement process improvements, ensuring the safety of our colleagues and minimizing disruption to daily operations.
Industrial or Distribution Automation
- Demonstrate a general understanding of distribution automation systems to effectively oversee and hold vendors accountable.
- Bring proven experience in projects involving automated material handling equipment, robotics, conveyor systems, and other mechanical components commonly used in distribution centers.
- Evaluate vendor proposals, ensuring compliance with specifications, and supervise the performance and maintenance of automation equipment.
- Stay up-to-date with industry emerging technologies and trends to drive innovation and exceed customer expectations.
Labor and Resource Planning
- Assess staffing requirements and determine the optimal allocation of labor to improve productivity while maintaining cost efficiency.
- Develop and implement labor standards and performance metrics to evaluate workforce performance and ensure alignment with productivity goals.
- Apply workload forecasting and planning techniques to ensure sufficient resources are available to meet varying demands.
Data Analysis, Reporting and Continuous Improvement
- Collect, analyze, and interpret key performance data (throughput, cycle times, service levels).
- Generate regular reports, offering insights to management on operational performance and improvement areas. Use data-driven analysis to identify trends and opportunities for continuous improvement.
- Encourage a culture of continuous improvement by involving colleagues in process enhancements.
- Lead or support improvement projects across teams using PPI Business System and Six Sigma methodologies.
Qualification
- Strong analytical and problem-solving skills, able to apply engineering principles to optimize processes and systems.
- Proficiency in process analysis tools and techniques, such as time and motion studies, process flow mapping, and statistical analysis.
- Knowledge of warehouse management systems (WMS), edge computing, and integrated workforce management solutions.
- Familiarity with labor management systems and the development of labor standards.
- Understanding of risk management, FMEA, and Hazard and Operability Analysis.
- Proficiency in data analysis and reporting, with the ability to generate actionable insights from sophisticated datasets.
- Experience in leading small to medium-sized projects.
- Ability to read electrical drawings and warehouse layouts